Overall Equipment Effectiveness (OEE) merupakan sebuah metrik inti yang sangat kuat dalam Total Productive Maintenance (TPM). OEE dapat memberikan nilai numerik untuk peluang peningkatan, mulai dari perhitungan ketersediaan kinerja, dan kualitas output dari peralatan tertentu.
Dalam industri manufaktur, menjaga efektivitas alat produksi adalah salah satu elemen utama yang menentukan keberhasilan operasional. Mesin yang tidak berjalan optimal dapat menimbulkan kerugian besar, mulai dari waktu henti produksi (downtime), produk cacat, hingga efisiensi kerja yang rendah. Oleh karena itu, Overall Equipment Effectiveness (OEE) menjadi metode pengukuran yang sangat penting untuk mengevaluasi kinerja alat produksi.
OEE tidak hanya sekadar angka untuk menunjukkan seberapa baik alat produksi bekerja, tetapi juga memberikan wawasan mengenai area mana yang membutuhkan perbaikan. Konsep ini merupakan bagian integral dari Total Productive Maintenance (TPM), sebuah pendekatan menyeluruh yang dirancang untuk memaksimalkan efisiensi peralatan. Dengan memadukan OEE ke dalam TPM, perusahaan dapat mengidentifikasi akar penyebab masalah, mengurangi kerugian produksi, dan memastikan proses berjalan lebih lancar. Artikel ini akan membahas secara mendalam penerapan OEE, mulai dari definisi, manfaat, hingga langkah-langkah implementasinya.
Pengertian Overall Equipment Effectiveness (OEE)
Overall Equipment Effectiveness atau OEE pertama kali diperkenalkan oleh Seiichi Nakajima pada tahun 1960 sebagai bagian dari konsep TPM. OEE adalah metode yang dirancang untuk mengevaluasi efektivitas alat produksi dengan cara mengukur tiga komponen utama, yaitu:
- Availability (Ketersediaan)
Mengukur waktu mesin yang benar-benar digunakan untuk produksi dibandingkan dengan waktu yang tersedia. Ini mencakup penghitungan waktu yang hilang akibat downtime, seperti kerusakan alat atau waktu pengaturan (setup time).
- Performance (Efisiensi Kinerja)
Mengukur kecepatan mesin bekerja dibandingkan dengan kecepatan idealnya. Faktor ini memperhitungkan kerugian akibat mesin berjalan lebih lambat dari yang seharusnya.
- Quality (Kualitas Produk)
Mengukur persentase produk yang memenuhi standar kualitas dibandingkan dengan total produk yang dihasilkan. Produk cacat, baik yang dibuang maupun yang harus diperbaiki, memengaruhi nilai kualitas.
Ketiga elemen ini saling terkait dan memberikan gambaran yang komprehensif tentang performa alat produksi. Selain untuk mengidentifikasi efisiensi mesin, OEE bisa menjadi petunjuk area area yang memerlukan perhatian untuk meningkatkan efektivitas keseluruhan. Berikut ini adalah beberapa manfaat dan tujuan dari penerapan OEE.
Cara Menghitung Overall Equipment Effectiveness
Cara menghitung Overall Equipment Effectiveness melibatkan penghitungan tiga elemen utama, yaitu Availability, Performance, dan Quality. Rumusnya adalah sebagai berikut:
OEE (%) = Availability (%) × Performance Efficiency (%) × Rate of Quality Product (%).
Setiap elemen ini dihitung menggunakan data operasional sebagai berikut:
- Availability (Ketersediaan)
Availability dihitung berdasarkan waktu kerja yang tersedia setelah dikurangi waktu henti (downtime).- Rumus:
Availability = (Waktu kerja yang tersedia – Waktu henti) / Waktu kerja yang tersedia × 100%. - Contoh Perhitungan:
Jika waktu kerja adalah 480 menit dan downtime adalah 30 menit (termasuk setup), maka:
Availability = (480 – 30) / 480 × 100% = 93.75%
- Rumus:
- Performance (Efisiensi Kinerja)
Performance mengukur kecepatan produksi aktual dibandingkan kecepatan ideal.- Rumus:
Performance = (Jumlah produk yang dihasilkan × Waktu ideal per unit) / Waktu kerja sebenarnya × 100%. - Contoh Perhitungan:
Jika mesin menghasilkan 400 produk dalam 450 menit dan waktu ideal per produk adalah 1 menit:
Performance = (400 × 1) / 450 × 100% = 88.89%
- Rumus:
- Quality (Kualitas Produk)
Quality dihitung berdasarkan rasio produk yang memenuhi standar dibandingkan total produk yang dihasilkan.- Rumus:
Quality = (Produk berkualitas / Total produk yang dihasilkan) × 100%. - Contoh Perhitungan:
Jika total produk adalah 400 dan jumlah produk cacat adalah 10, maka:
Quality = (400 – 10) / 400 × 100% = 97.5%
- Rumus:
Berdasarkan contoh di atas, OEE dihitung sebagai berikut:
OEE = 93.75% × 88.89% × 97.5% = 81.13%
Nilai OEE ideal adalah 85% atau lebih, yang menunjukkan bahwa alat produksi berfungsi secara optimal.
Manfaat dan Tujuan Penerapan OEE
Tujuan utama penerapan Overall Equipment Effectiveness adalah untuk memastikan empat tujuan utama dari OEE, yakni zero accident, zero breakdown, zero crisis, dan zero defect. Bagian Produksi, Pemeliharaan (maintenance), dan Rekayasa (engineering) harus membentuk kerja sama yang efektif serta efisien. Sedangkan Operator sebagai pengendali mesin, harus bisa meningkatkan rasa “kepemilikan” terhadap peralatan.
Penerapan OEE bertujuan untuk memberikan sejumlah manfaat bagi perusahaan manufaktur, di antaranya:
- Mengidentifikasi Kerugian Produktivitas
OEE membantu mengungkap kerugian yang sebelumnya tersembunyi, seperti downtime yang tidak terencana, lambatnya proses produksi, atau produk cacat. Dengan identifikasi ini, perusahaan dapat fokus pada perbaikan yang paling dibutuhkan.
- Penentuan Titik Awal Kinerja
OEE menyediakan data yang menjadi baseline untuk mengevaluasi peningkatan kinerja alat produksi dari waktu ke waktu.
- Membandingkan Performa Lintas Departemen
OEE memungkinkan perusahaan untuk membandingkan efisiensi di berbagai lini produksi atau departemen, sehingga dapat mengarahkan sumber daya ke area yang memerlukan perbaikan paling signifikan.
The Six Big Losses of Overall Equipment Effectiveness
Kerangka Overall Equipment Effectiveness juga digunakan untuk mengidentifikasi Six Big Losses atau enam kerugian besar, yaitu enam kategori kerugian produktivitas yang paling umum terjadi dan kini bertambah menjadi 7 poin inti.
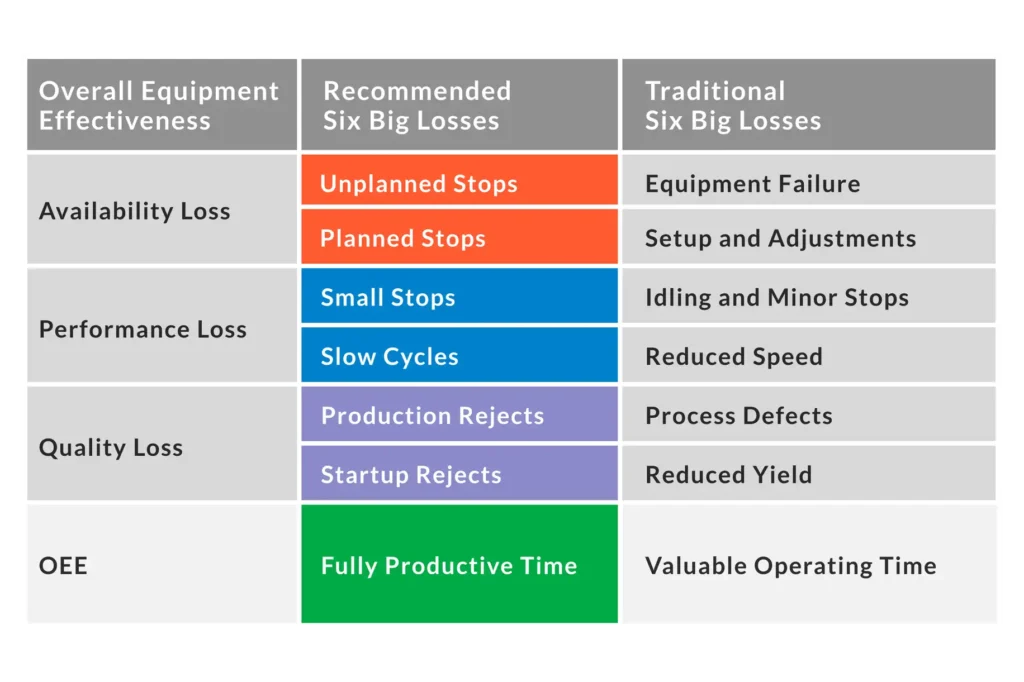
- Equipment Failure (Kerusakan Alat): Kerugian akibat kerusakan alat atau downtime yang tidak terencana.
- Setup and Adjustments (Pengaturan dan Penyesuaian): Waktu yang hilang untuk setup, perubahan produk, atau penyesuaian alat.
- Idling and Minor Stops (Henti Sebentar): Gangguan kecil seperti material jam atau sensor yang tidak sejajar.
- Reduced Speed (Kecepatan Berkurang): Mesin berjalan lebih lambat dari kecepatan idealnya.
- Process Defects (Cacat Proses): Produk cacat yang dihasilkan selama proses stabil.
- Reduced Yield (Hasil Rendah): Produk cacat yang dihasilkan selama startup alat produksi.
Tantangan dalam Penerapan OEE
OEE dapat mengemas banyak informasi menjadi satu ukuran yang membuat metode perhitungan ini menjadi sangat kuat. Di samping itu, kekuatannya ini bisa menyulitkan penghitungan dan membingungkan untuk ditafsirkan.
Pengguna biasanya mendapat masalah saat mereka mencoba untuk:
- Menggunakan OEE terutama sebagai KPI tingkat tinggi (indikator kinerja utama)
- Melihat OEE sebagai ukuran eksternal yang memiliki arti bagi pelanggan
- Memperbanyak OEE di beberapa mesin di departemen atau pabrik
- Menghitung OEE pada setiap peralatan
- Mengukur diri mereka dengan ukuran OEE “kelas dunia”
- Fokus pada angka demi angka itu sendiri daripada konteks peningkatan
- Menggunakan OEE sebagai klub, bukan sebagai tolok ukur
Langkah-Langkah Implementasi OEE
Untuk itu, dibutuhkan beberapa langkah yang tepat sebagai tips dalam mengimplementasikan Overall Equipment Effectiveness. Berikut adalah delapan langkah penting untuk menerapkan OEE secara efektif di perusahaan:
- Pilih mesin yang paling sering digunakan untuk analisis awal.
- Susun definisi OEE yang jelas, termasuk parameter waktu dan jenis kerugian.
- Tetapkan metode pengumpulan data OEE yang sistematis dan melibatkan operator.
- Berikan pelatihan kepada tim mengenai pentingnya OEE.
- Kumpulkan data secara konsisten dari proses produksi.
- Proses dan analisis data secara langsung untuk memberikan umpan balik harian.
- Gunakan metode visual untuk menyampaikan hasil analisis kepada tim operasional.
- Libatkan manajemen untuk memastikan dukungan dan kelanjutan program.
Kesimpulan
Overall Equipment Effectiveness adalah alat penting untuk meningkatkan efektivitas alat produksi dalam industri manufaktur. Dengan menganalisis data OEE, perusahaan dapat mengidentifikasi kerugian utama, meningkatkan efisiensi, dan memastikan kualitas produk yang konsisten.
Mengintegrasikan OEE ke dalam Total Productive Maintenance memungkinkan perusahaan untuk secara proaktif mengelola peralatan mereka, mengurangi downtime, dan meningkatkan daya saing di pasar. Temukan cara paling efektif untuk meningkatkan performa dalam penerapan Total Quality Maintenance yang berfokus menekan angka kecacatan produk sampai level zero dan menunjang peningkatan angka Overall Equipment Effectiveness (OEE) dalam pelatihan Quality Maintenance bersama PQM Consultants.
Dapatkan wawasan khusus tentang Quality Maintenance paling efektif yang akan memberikan dampak signifikan bagi peningkatan bisnis melalui program “Achieving Zero Defect with Quality Maintenance Implementation”.
Referensi
- Shiftindonesia.com. 8 Langkah untuk Sukses Menerapkan OEE.
- Scmguide.com. Cara Menghitung Overall Equipment Effectiveness (OEE).
- Oee.com. Six Big Losses. diakses dari https://www.oee.com/oee-six-big-losses/